Leading Techniques for Optimizing Steel Manufacture Processes for Maximum Performance
In the realm of steel fabrication, the quest of performance is a perpetual goal that drives sector professionals to discover ingenious techniques and innovations. As the need for accuracy and rate heightens, firms are obliged to reassess their construction processes continuously. From precise design preparing to embracing innovative modern technologies, the pursuit for maximum effectiveness in steel fabrication involves a diverse technique. By implementing top strategies tailored to optimize operations, services not just boost efficiency yet additionally raise the top quality of their outcome. Allow's check out exactly how these strategies can change steel fabrication processes, leading the way for unprecedented performance and competition in the market.
Efficient Format Preparation
In the world of steel manufacture procedures, effective and calculated layout preparation plays a critical duty in streamlining production operations and taking full advantage of functional efficiency. The design of a steel construction facility straight affects the effectiveness of procedures, material flow, and worker performance. By meticulously designing the plan of equipment, workstations, storage space areas, and product handling devices, business can significantly minimize unnecessary movement, reduce material taking care of times, and maximize the general production procedure.
An effective format strategy thinks about aspects such as operations series, closeness of workstations, product handling courses, and security laws. It intends to create a streamlined and rational circulation of activities from resources consumption to the last item send off. With reliable layout planning, companies can eliminate traffic jams, reduce manufacturing downtime, and boost the general operational efficiency of the steel fabrication process.
In addition, a well-balanced layout plan enables much better utilization of readily available area, boosted communication between employees, and enhanced security techniques within the facility. On the whole, spending time and sources in establishing a reliable format strategy can generate significant benefits in regards to raised performance and expense financial savings for steel construction businesses.
Advanced Reducing Technologies
Using advanced innovations in steel manufacture processes enhances precision, performance, and general manufacturing quality. Advanced reducing modern technologies play a critical function in simplifying operations and maximizing the construction process. Among the most noticeable improvements in this field is the execution of laser cutting systems. Laser reducing deals unequaled precision, enabling intricate forms and elaborate designs to be cut with minimal product wastage. In addition, plasma reducing technology has likewise revolutionized steel fabrication by making it possible for swift and accurate puncturing electrically conductive materials. This technique is particularly reliable for reducing thick steel plates with speed and accuracy. Water jet cutting is one more innovative innovation that makes use of a high-pressure stream of water to cut with different kinds of products, consisting of steel, with phenomenal accuracy. By integrating these sophisticated cutting innovations into steel fabrication procedures, producers can considerably boost effectiveness, reduce manufacturing times, and ultimately enhance the high quality of their products.
Automated Welding Solutions
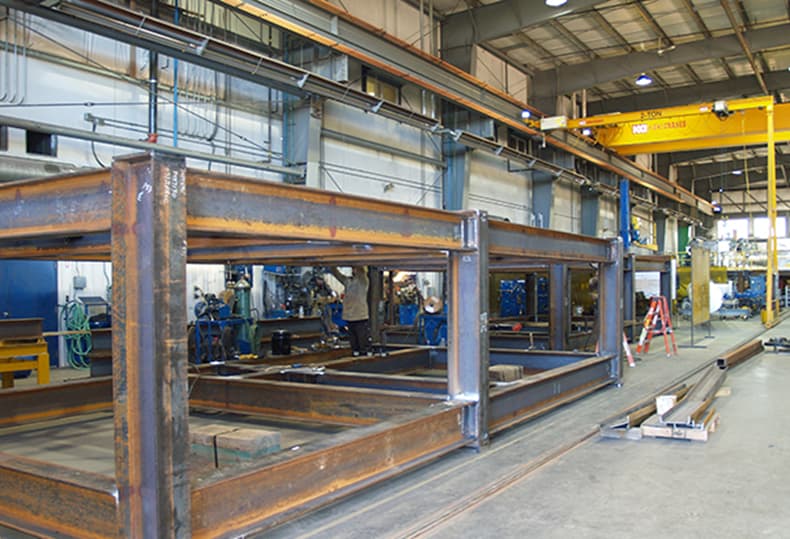
One of the key benefits of automated welding systems is their capability to his explanation keep a high degree of precision throughout the welding process. The accuracy provided by these systems makes certain that welds are consistent and meet the required requirements, bring about stronger and extra dependable metal structures. Furthermore, automated welding systems decrease the risk of human error, causing fewer problems and rework.
Additionally, these systems can take care of intricate welding jobs effortlessly, including welding in limited rooms or on curved surfaces. This convenience makes automated welding systems appropriate for a vast variety of steel fabrication applications, from large-scale commercial tasks to intricate customized styles. On the whole, the implementation of automated welding systems in steel construction processes dramatically enhances efficiency, quality, and overall project outcomes.
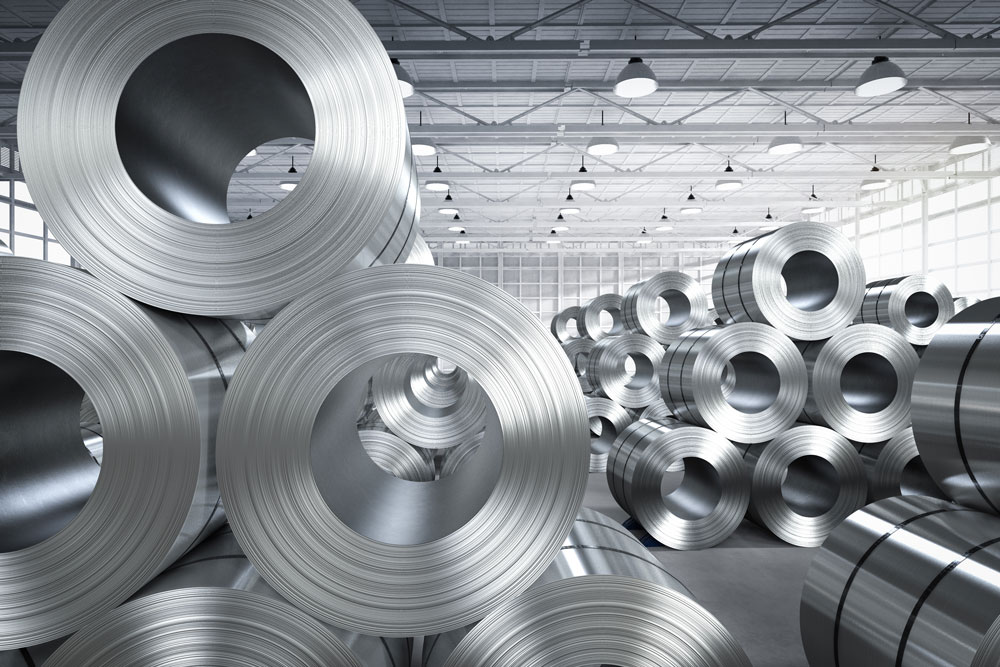
Supply Administration Solutions
Enhancing functional performance and simplifying procedures, reliable stock management remedies play a vital function in enhancing steel manufacture procedures. By executing robust inventory administration systems, steel fabrication companies can ensure that the ideal materials are offered when needed, minimizing disturbances and hold-ups in manufacturing timetables. Utilizing advanced software remedies permits for real-time monitoring of stock degrees, allowing accurate projecting of product demands and protecting against stockouts or overstock situations.
In addition, supply monitoring remedies assist in decreasing carrying prices associated with excess stock and improve money circulation by lining up stock degrees with real demand. By categorizing products based upon usage regularity and urgency, makers can focus on procurement and storage area allotment, further enhancing operational performance. Furthermore, executing barcode or RFID innovation facilitates precise supply monitoring and streamlines the monitoring of product motions within the facility.
Continual Process Improvement
To build recommended you read on the gains made via efficient inventory monitoring solutions, the focus currently shifts in the direction of driving constant procedure renovation within steel fabrication operations. Constant procedure improvement is a systematic strategy intended at improving effectiveness, lowering waste, and raising overall top quality throughout the manufacture procedure. By implementing a society of continuous improvement, steel manufacture companies can recognize bottlenecks, improve process, and optimize resources to optimize productivity.
One secret aspect of constant process enhancement in steel fabrication is the routine evaluation and analysis of manufacturing procedures. This includes celebration responses from employees, monitoring vital performance signs, and recognizing areas for enhancement. By leveraging data-driven insights, business can make enlightened choices to drive purposeful adjustments that positively affect procedures.
Moreover, taking on lean production principles can substantially add to refine improvement in steel fabrication. steel fixing. Strategies such as worth stream mapping, five organization, and Kaizen occasions can assist remove non-value-added activities, systematize procedures, and promote a culture of development and continual learning within the company
Conclusion
In final thought, optimizing steel construction procedures for maximum efficiency needs mindful planning, making use of advanced cutting important site innovations, applying automated welding systems, handling inventory effectively, and continually boosting procedures. By integrating these approaches, producers can enhance productivity, minimize expenses, and enhance general efficiency in the steel manufacture market.
With effective layout planning, companies can eliminate bottlenecks, lower manufacturing downtime, and improve the overall functional effectiveness of the steel fabrication procedure. steel fabrication melbourne.
Making use of advanced technologies in steel construction processes enhances accuracy, effectiveness, and general production quality. By integrating these advanced reducing technologies into steel manufacture procedures, suppliers can considerably enhance performance, decrease manufacturing times, and inevitably boost the quality of their products.
In general, the implementation of automated welding systems in steel manufacture procedures significantly improves efficiency, top quality, and overall job outcomes.
One key facet of continuous procedure improvement in steel fabrication is the normal evaluation and analysis of manufacturing procedures. (Alpha reo)